7.2.2. Образцы насыщают водой в соответствии с разд.2 или 3. Образцы керамических изделий перед водонасыщением высушивают до постоянной массы. Образцы силикатных изделий после водонасыщения взвешивают.
Допускается использовать образцы непосредственно после определения их водопоглощения.
7.2.3. Замораживание образцов в морозильной камере и оттаивание их в воде осуществляют в контейнерах.
Горизонтальные зазоры между образцами в контейнерах должны быть не менее 20 мм. При укладке образцов в контейнеры до трех рядов по высоте вертикальные зазоры между рядами, образуемые прокладками, должны быть не менее 20 мм. При большем числе рядов по высоте зазоры между рядами должны быть не менее 50 мм.
Загрузка камеры образцами не должна превышать 50% ее полезного объема.
7.3. Проведение испытания
7.3.1. Температура воздуха морозильной камеры до загрузки образцами должна быть не выше минус 15 °С, а после загрузки не должна превышать минус 5 °С. Началом замораживания образцов считают момент установления в камере температуры минус 15 °С. Температура воздуха в камере от начала до конца замораживания должна быть от минус 15 до минус 20 °С.
7.3.2. Продолжительность одного замораживания образцов должна быть не менее 4 ч. Перерыв в процессе одного замораживания не допускается.
7.3.3. После окончания замораживания образцы в контейнерах полностью погружают в сосуд с водой температурой (20±5) °С, поддерживаемой термостатом до конца оттаивания образцов.
Продолжительность оттаивания должна быть не менее половины продолжительности замораживания.
7.3.4. Одно замораживание и последующее оттаивание составляют один цикл, продолжительность которого не должна превышать 24 ч.
7.3.5. При окончании испытания на морозостойкость или его временном прекращении образцы после оттаивания хранят в ванне с гидравлическим затвором. При возобновлении испытания образцы дополнительно водонасыщают в соответствии с разд.2 или 3 (без высушивания образцов керамических изделий и взвешивания силикатных после водонасыщения).
7.3.6. При оценке морозостойкости по степени повреждений после проведения требуемого числа циклов замораживания - оттаивания производят визуальный осмотр образцов и фиксируют появившиеся дефекты.
7.3.7. При оценке морозостойкости по потере массы после проведения требуемого числа циклов замораживания - оттаивания образцы керамических изделий высушивают до постоянной массы, а образцы силикатных изделий насыщают водой в соответствии с разд.2 или 3.
7.3.8. При оценке морозостойкости по потере прочности при сжатии после проведения требуемого числа циклов замораживания - оттаивания опорные поверхности каждого образца в отдельности (в том числе контрольных) выравнивают цементным раствором по приложению 2 ГОСТ 8462. Допускается не выравнивать опорные поверхности образцов силикатных изделий и керамических, изготовленных методом прессования, при отсутствии на них неровностей, вздутий, шелушений и т.п.
Образцы насыщают водой в соответствии с разд.2 или 3 и проводят испытание на сжатие каждого образца в отдельности по разд.3 ГОСТ 8462.
7.4. Обработка результатов
7.4.1. После визуального осмотра образцов делают заключение о соответствии их степени повреждений требованиям НТД на изделия конкретных видов.
7.4.2. Потерю массы (
) образцов керамических изделий в процентах вычисляют по формуле

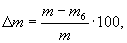
где
масса образца, высушенного до постоянной массы после требуемого числа циклов замораживания-оттаивания, г.

Потерю массы образцов силикатных изделий в процентах вычисляют по формуле

Где
масса образца, насыщенного водой после требуемого числа циклов замораживания-оттаивания, г.

За значение потери массы изделий принимают среднее арифметическое результатов определений потери массы всех образцов, рассчитанное с точностью до 1%.
7.4.3. Потерю прочности (
) изделий при сжатии в процентах вычисляют с точностью до 1% по формуле


где
среднее арифметическое пределов прочности при сжатии контрольных образцов, МПа;


7.4.4. Исходные данные и результаты контроля морозостойкости заносят в журнал испытаний. В журнале должно быть указано:
наименование изделия, марка по прочности, дата испытания;
метод контроля морозостойкости (объемный, односторонний);
размеры каждого образца;
описание дефектов, обнаруженных на каждом образце перед испытанием;
температура замораживания и длительность снижения температуры в морозильной камере до минус 15 °С после загружения ее образцами;
описание появившихся дефектов, обнаруженных на каждом образце при осмотрах в процессе испытания;
масса каждого образца до и после испытания и потеря массы;
пределы прочности при сжатии каждого из испытанных образцов и потеря прочности;
число циклов замораживания - оттаивания образцов.
8. Контроль морозостойкости при одностороннем замораживании
Методы контроля морозостойкости при объемном и одностороннем замораживании не взаимозаменяемы.
8.1. Средства испытания
Холодильно-дождевальная установка (ХДУ), основные технические характеристики которой приведены в приложении 2.
Допускается применение морозильной камеры по п.7.1 со следующими приспособлениями и оборудованием:
аппарат для одностороннего замораживания образцов (АДОЗО), основные технические характеристики которого приведены в приложении 2, или рама запорная теплоизолирующая съемная сквозная;
установка дождевальная.
Пластины резиновые ОМБ5 или ОМБ10 по ГОСТ 7338.
Сосуд с решеткой.
Электрошкаф сушильный по ТУ 16-681.032 или любой другой конструкции с автоматической регулировкой температуры в пределах 100-110 °С.
Ванна с гидравлическим затвором по п.7.1.